INDUROS 1300
Your superior AMR solution for intralogistics and logistics - indoor and outdoor
The Innok Robotics innovation 2025: The INDUROS 1300.
For all those who need even more power and traction. Our autonomous mobile transport robot that can be used indoors and outdoors. This makes it possible for the first time to achieve end-to-end automation in material transport, even in brownfield production sites (production and logistics halls and outdoor areas) and, for example, from one hall to another via outdoor areas. Innok customers use the INDUROS to pull pallet trolleys, mesh boxes and other material trolleys and containers on four wheels. The INDUROS 1300 as an AMR (autonomous mobile robot, also known as an automated guided vehicle or AGV) also replaces the classic manual tugger train for numerous customers – but fully autonomously. This is where you will find the INDUROS 700 with up to 700 kg of pulling force.
Our latest INDUROS white paper is here!
Automation is not just the future - it is the solution to current economic challenges.
But how much potential is there really in autonomous transport robots? Our exclusive whitepaper shows you how Innok customer Rigdon revolutionized their processes by using the INDUROS transport robot and saved €120,000 and more per year per robot - without expensive conversions to existing buildings or complex IT integrations!
The INDUROS is an autonomous mobile transport robot that transports components and products both indoors and outdoors.
It also masters combined indoor and outdoor applications: If your operational process to be automated begins with freshly produced components from pre-production (e.g. the bar turning shop), but further mechanical processing (e.g. CNC milling) continues in another production hall, the Innok INDUROS is the right - and probably the only - robot for this transport task.
10 years of experience in industry and logistics
INDUROS is the specialist for fully autonomous operation. As a German manufacturer, Innok Robotics has more than 10 years of experience in this field in industry and logistics.
At the customer's request, remote-controlled or semi-automatic operation is also possible with this AMR. No artificial orientation aids such as transponders in the floor or similar, as with older driverless transport systems (AGVs), are required for navigation.
The market-leading sensor concept enables the INDUROS to be used flexibly and with little effort at different work locations.
Very short amortization times
The proprietary Innok COCKPIT™ autonomy software developed by Innok Robotics and used in all mobile robots is easy to use and enables individual routes to be recorded and defined. It can be used efficiently by the user themselves after a short training period.
The INDUROS is a proven, reliable autonomous system. Depending on the shift model, very short amortization times are achieved (in three-shift operation and forklift trucks as a manual solution: 1 to 2 years max.). External markings or installations are not required for the INDUROS.
More safety on the factory premises
The all-electric drive technology (Power Li battery, up to 4 electric motors per vehicle) achieves zero CO₂ emissions locally, which reduces your company's carbon footprint.
The safety of people and property on the factory premises is significantly improved by using an INDUROS compared to a manual process (especially with the help of forklift trucks).
The INDUROS missions can start on an ad hoc or time-related basis, can be planned and are very reliable, e.g. via intra-logistics stations.
INDUROS video gallery - Features and customer testimonials
You can find a selection of current product videos and customer testimonials here. For specific use cases and customer solutions, visit our Use Cases.
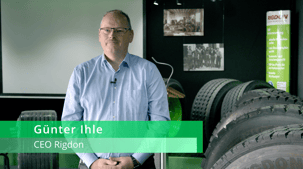
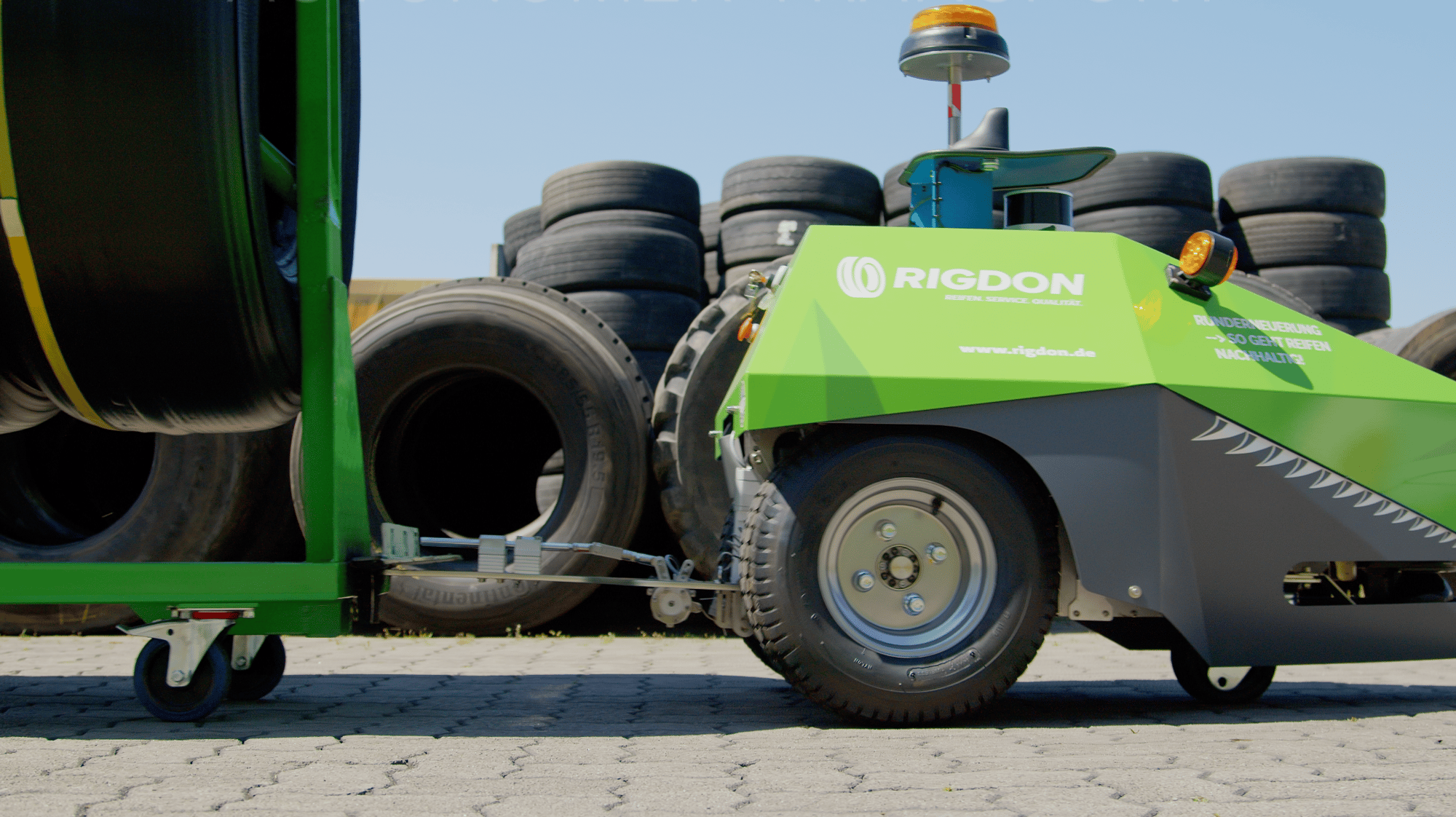
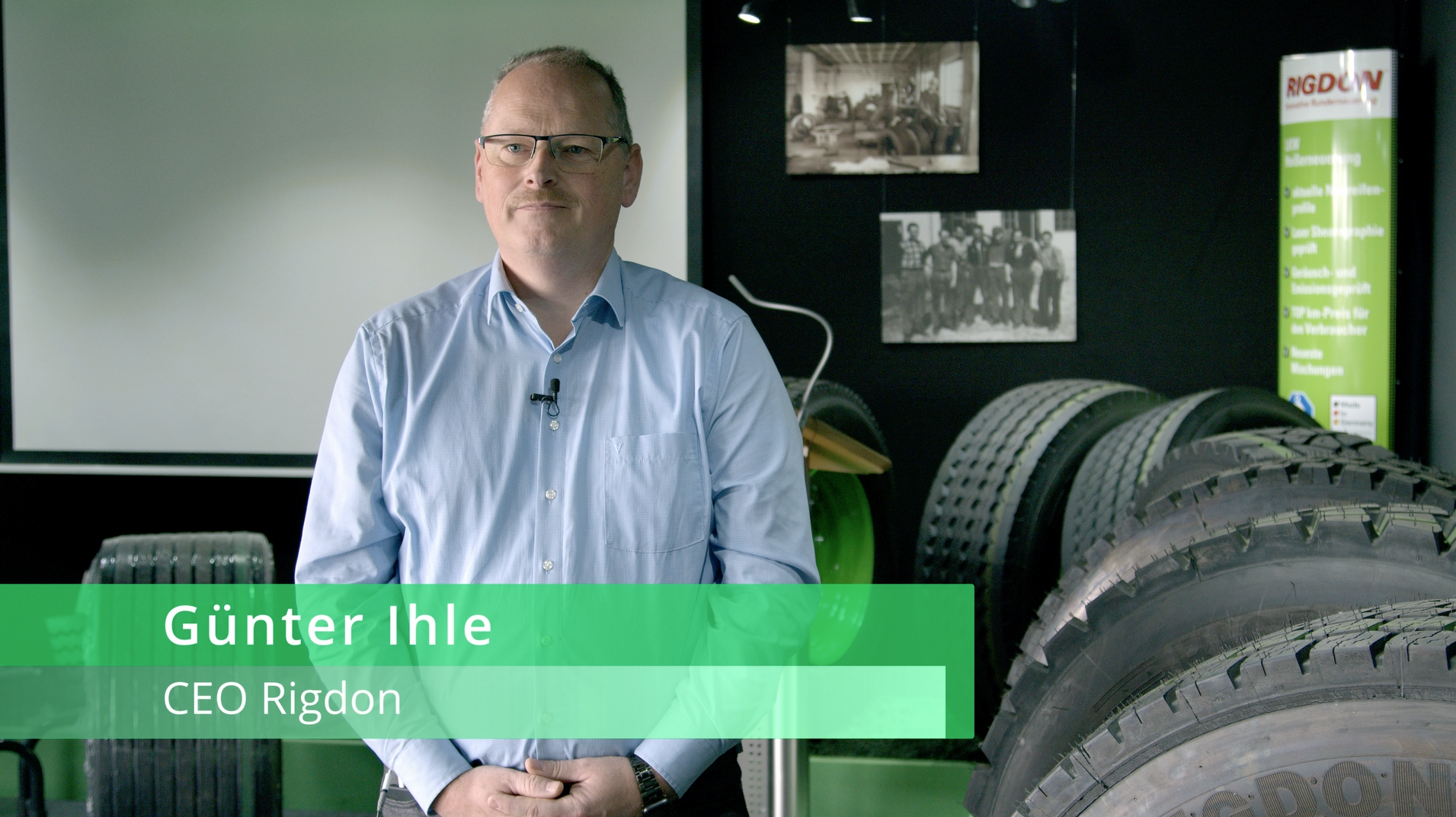
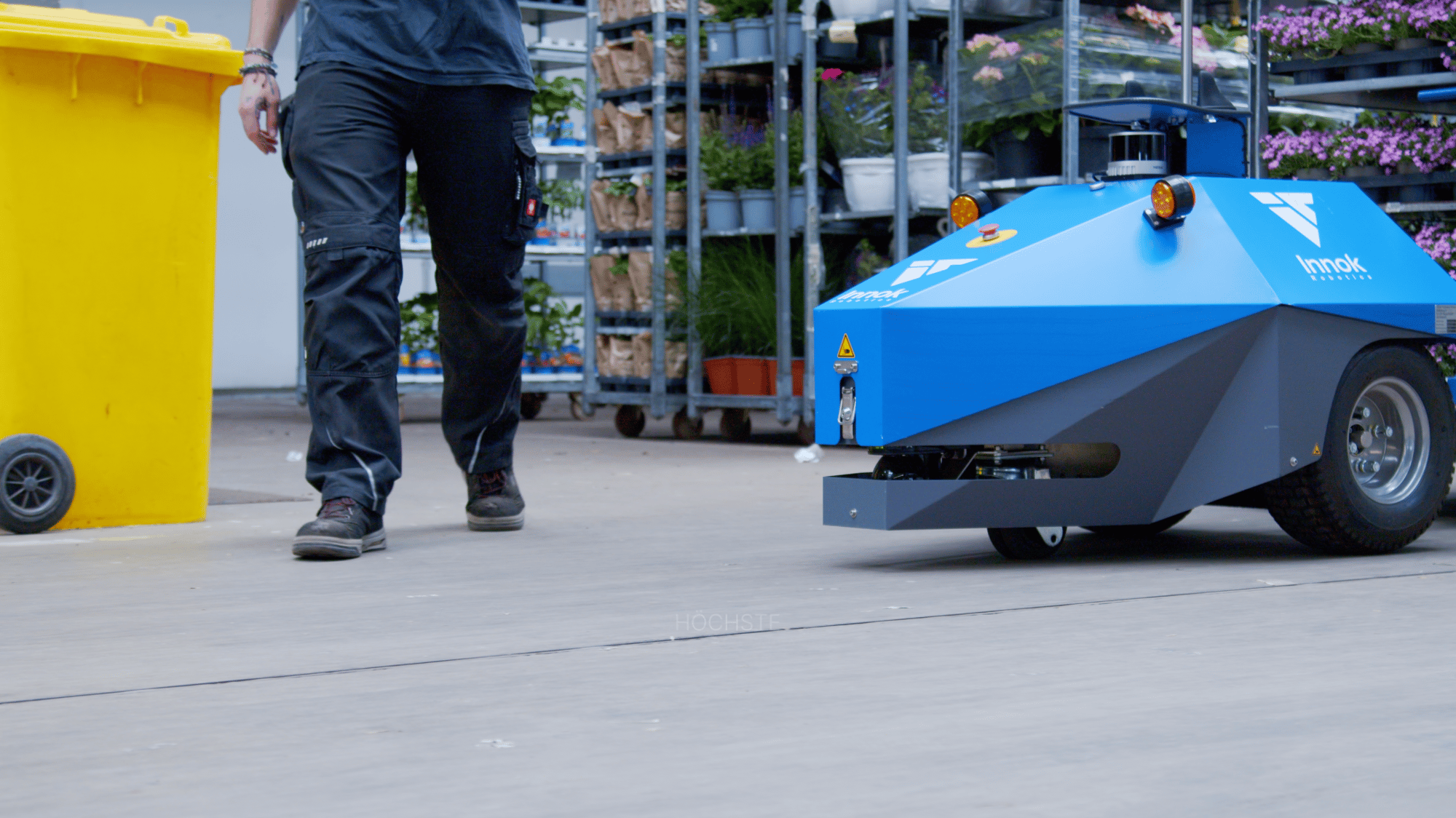
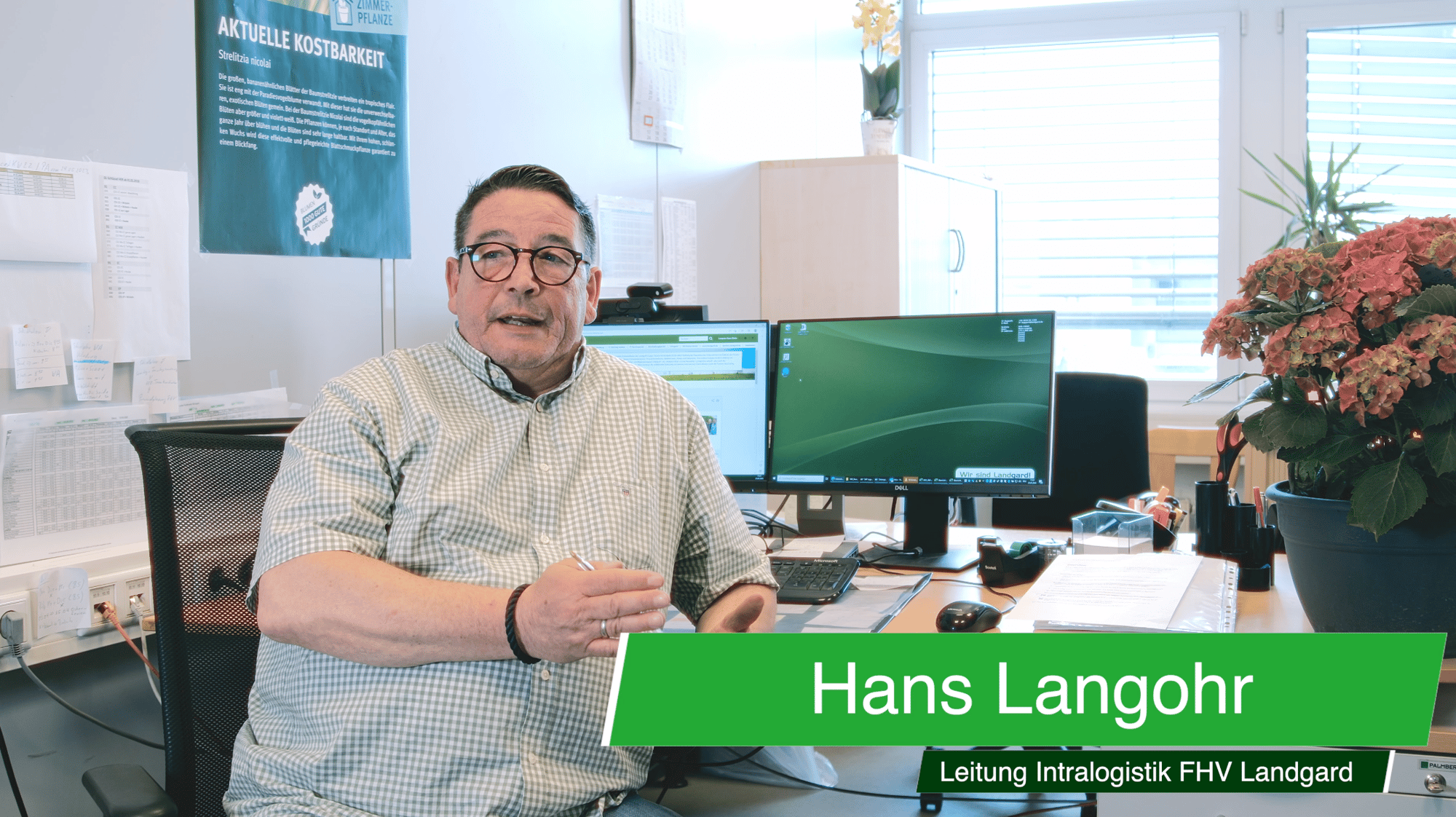
AMR features
One robot - many faces:
So compact and yet so powerful! The INDUROS can be used in many different ways thanks to its autonomous features. Innok customers use the INDUROS to pull pallet trucks, pallet cages and even large waste containers on 4 wheels. As an automated guided vehicle system (AGV), the INDUROS also replaces the classic tugger train for many customers - but fully autonomously.
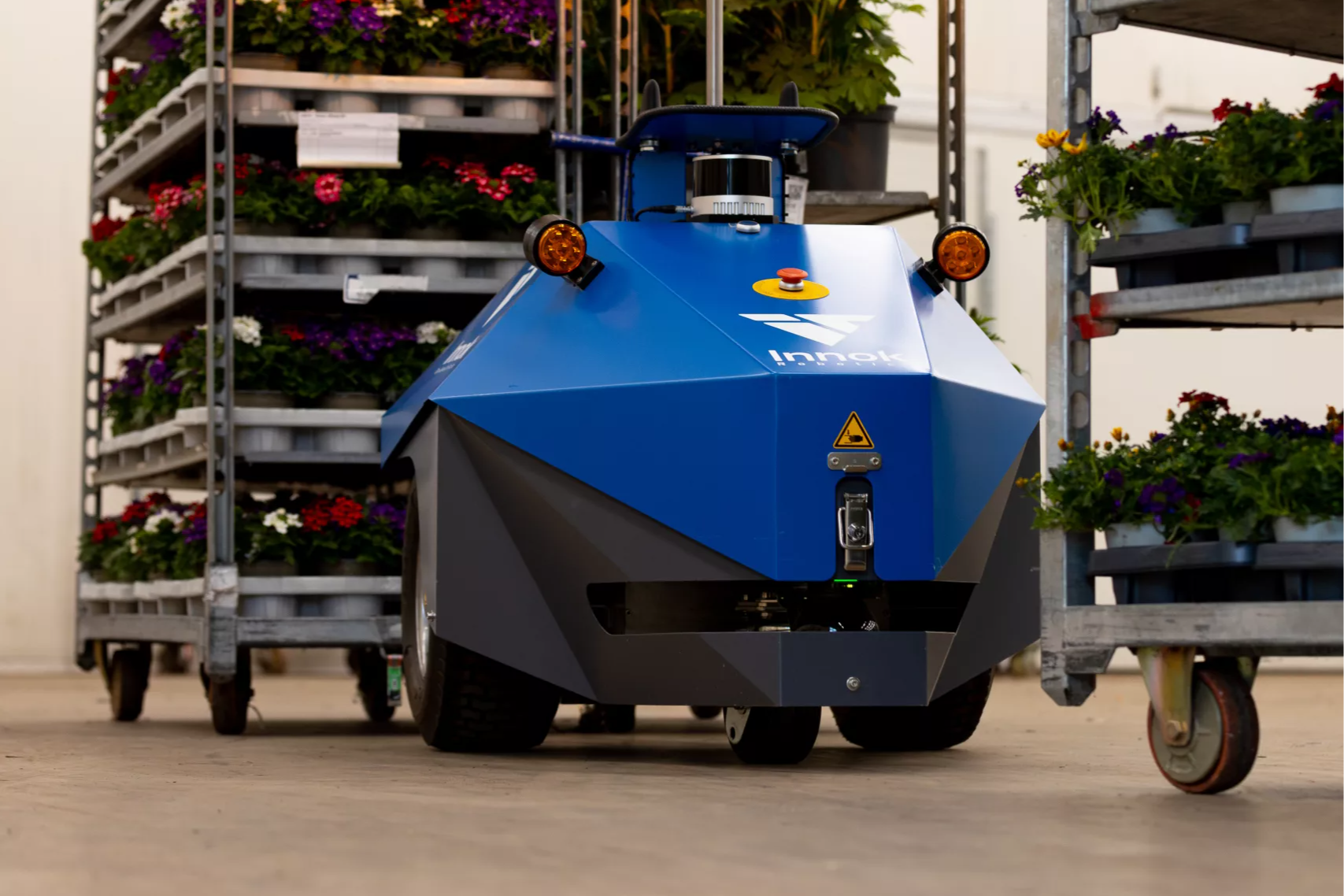
Tight turning circle,
low space requirement
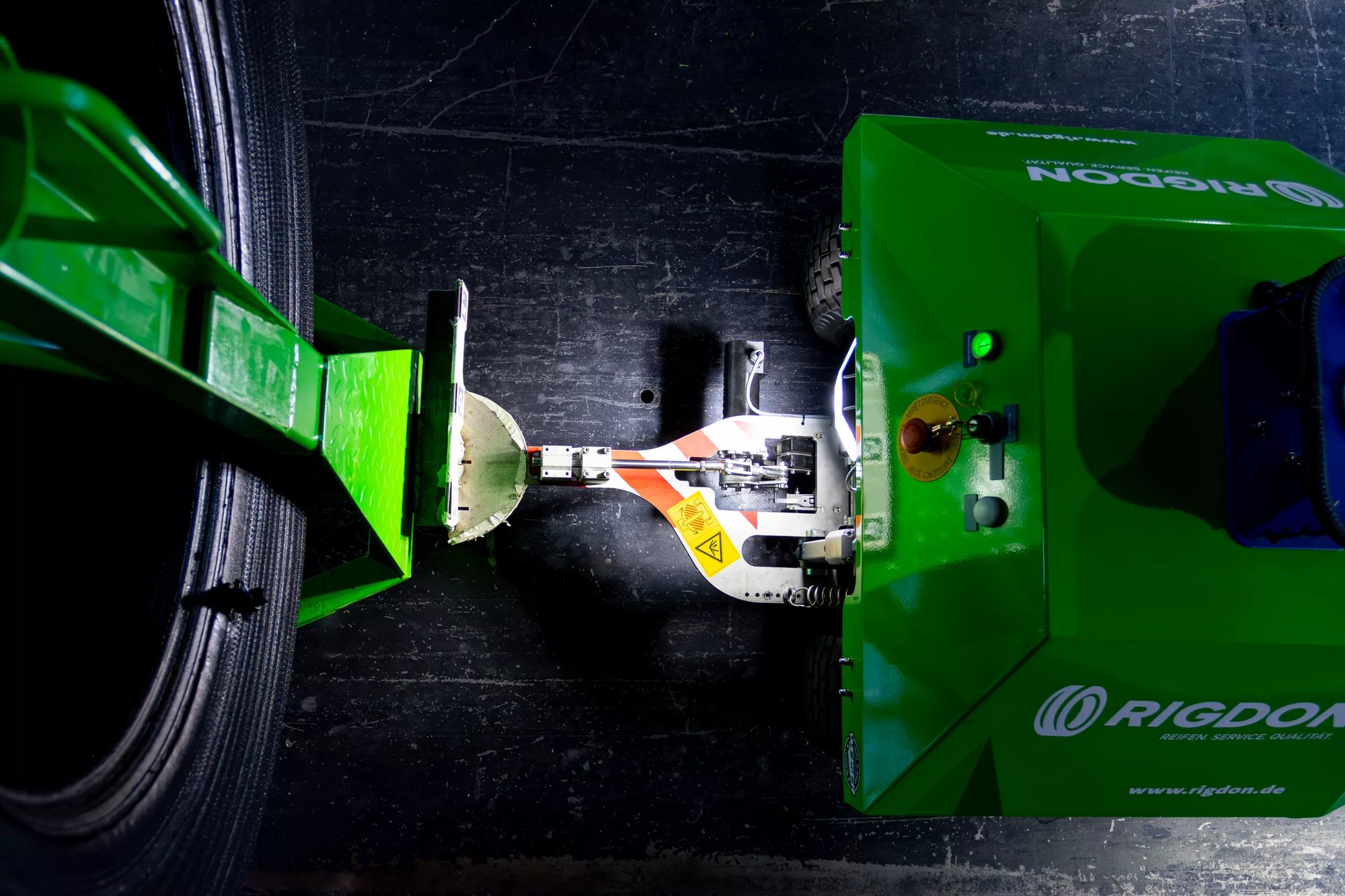
trailer coupling
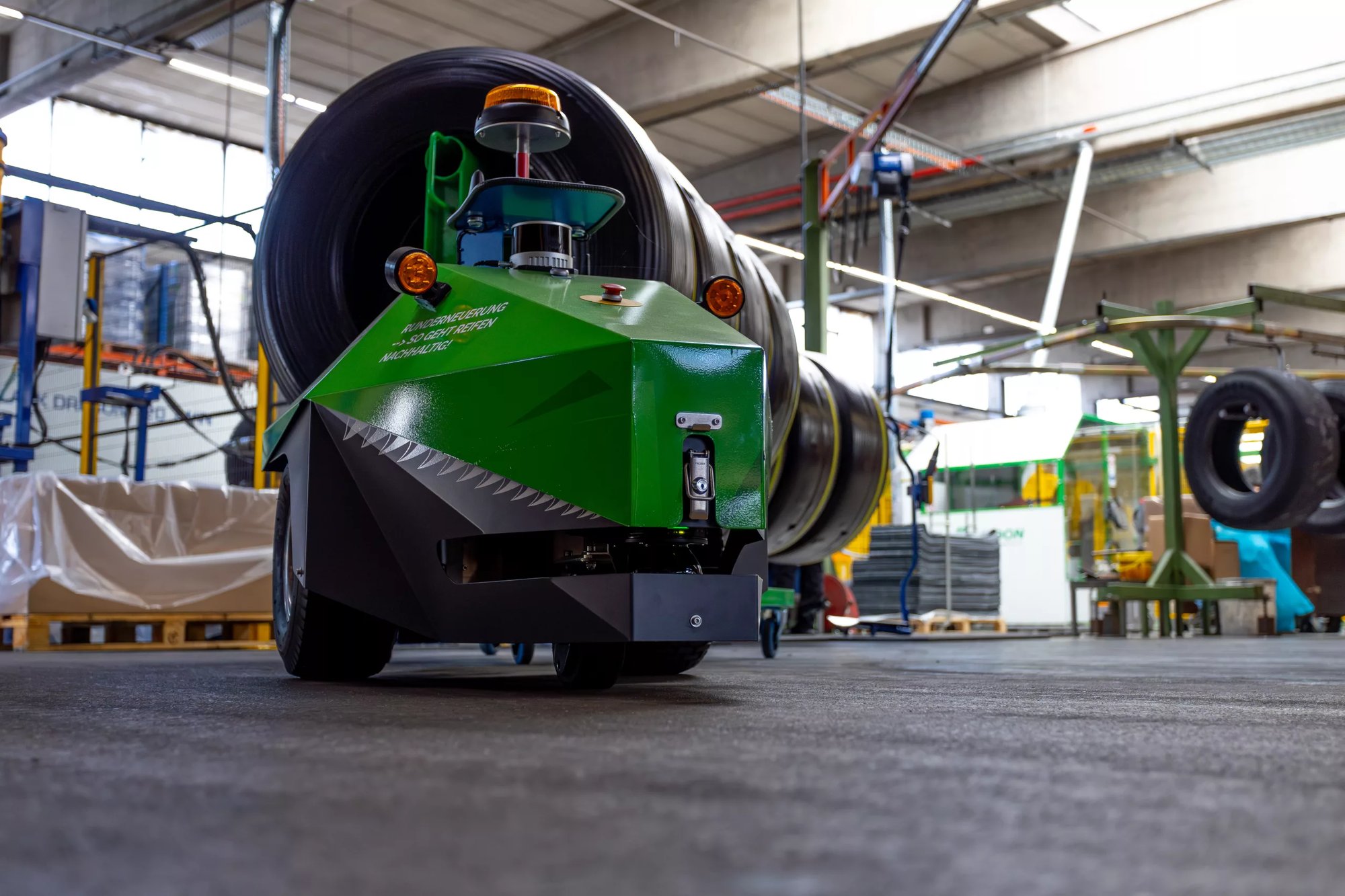
transport robot
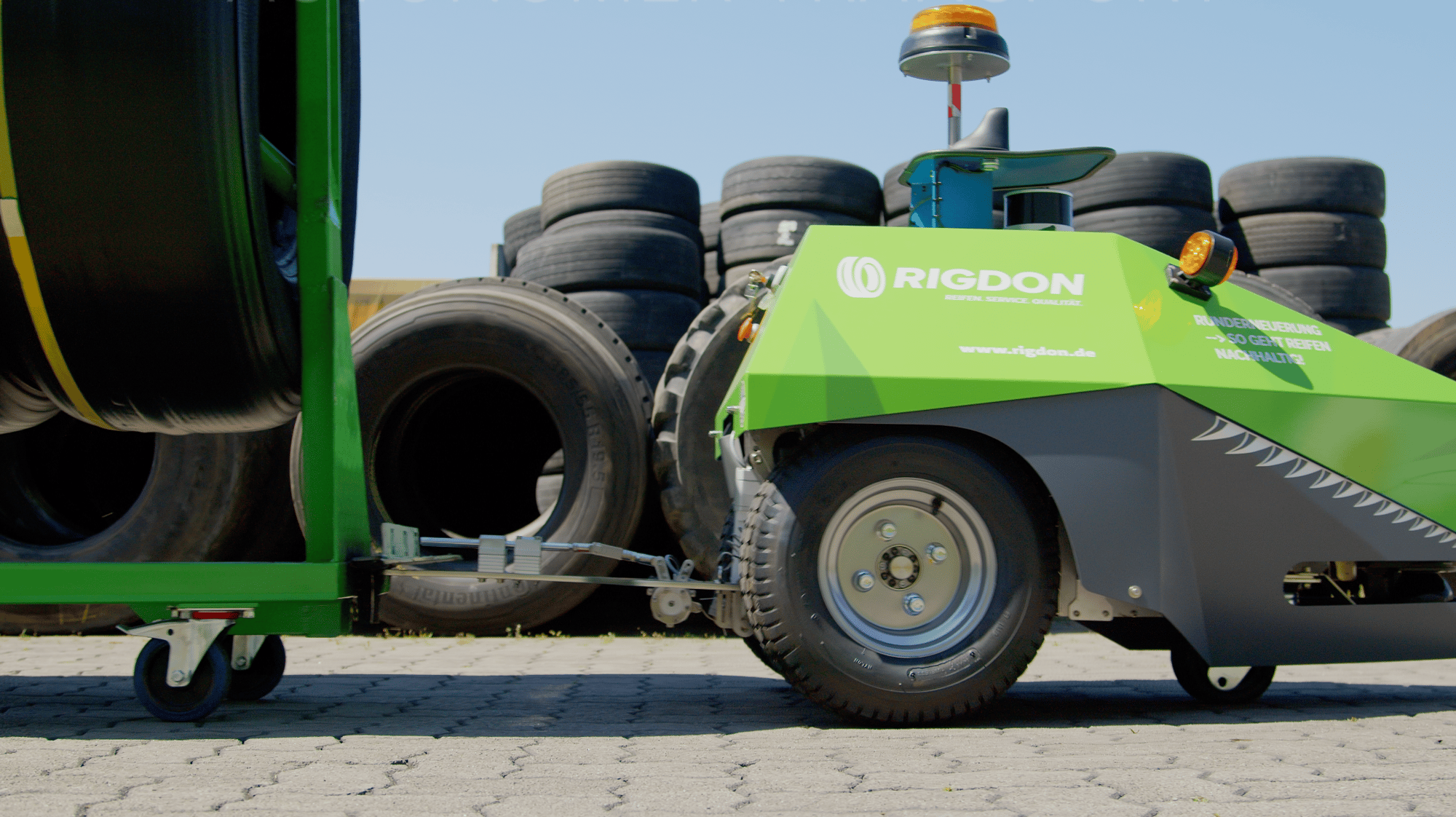
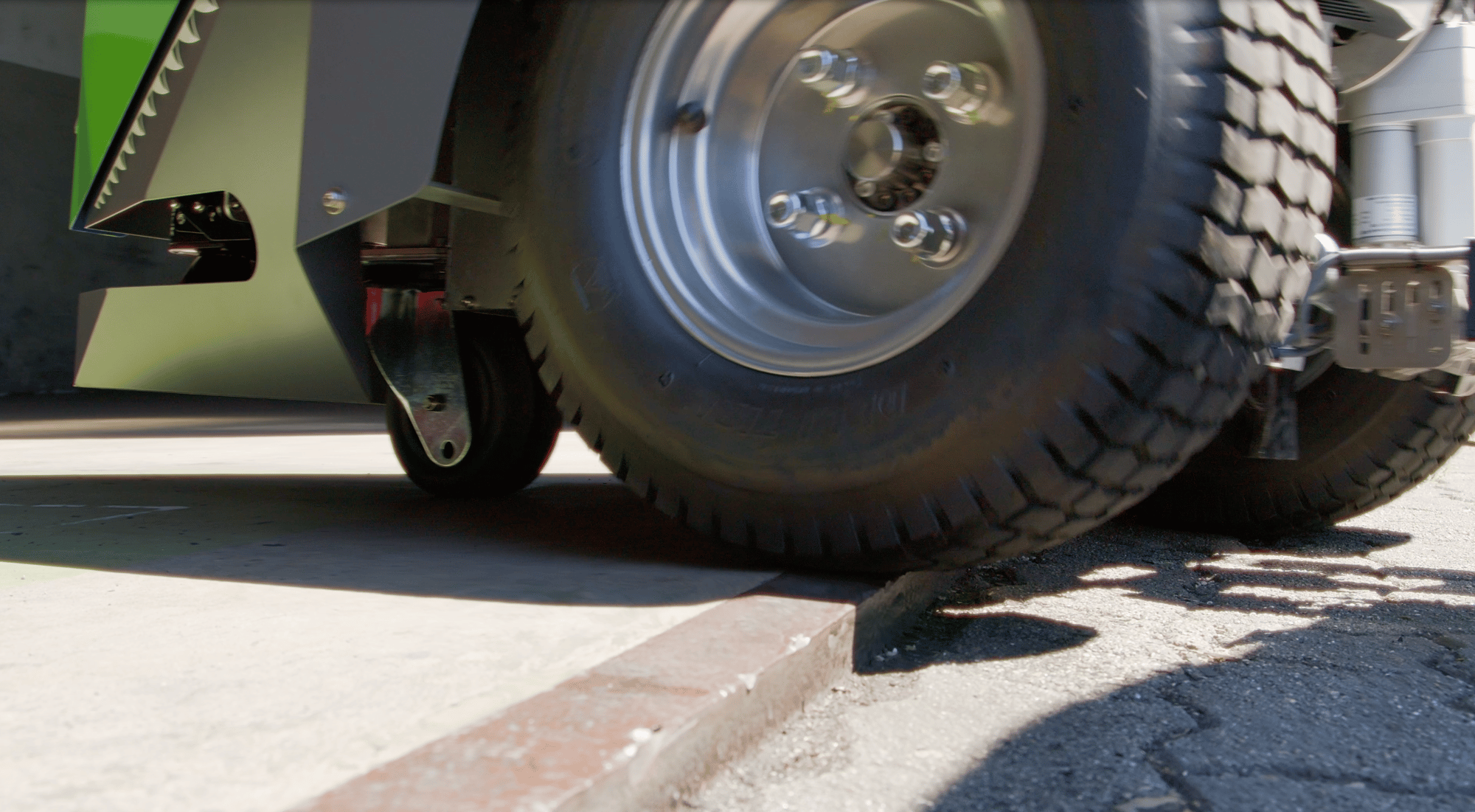
INDUROS 1300
in action
The transport robot is compact and agile and can therefore also maneuver in confined spaces. Thanks to its robust design, the INDUROS 1300 can be used both indoors and outdoors. The powerful 1500 W drive allows a trailer load of up to 1300 kg. If a tractive force of up to 700 kg is required, we recommend our INDUROS 700.
Technical data
Dimensions: 115 x 80 x 100 cm
Weight: approx. 300 kg
Towing capacity (depending on ground conditions, incline and speed): up to 1300 kg
Track width: 57 cm
Ground clearance: 10 cm
Maximum speed: 3.2 km/h or 0.9 m/s or 6.5 km/h or 1.8 m/s depending on load weight
Ambient temperature: -10 °C to +45 °C
Charging time: 2 hours (20 to 80 %)
Battery life: up to 16 hours
Battery: 2900 Wh, 48 V, up to 4.0 kW
Drive wheels: Ø 41 cm, steel rims, turf profile
Motor: 1500 W, gear ratio: 1:100, optionally 1:50
Steering system: differential steering
Protection class: IP65
Radio networks: WLAN or LTE
Ignite the turbo in logistics now with the INDUROS 1300
FAQ
-
How does the installation work?
- Step 1: Mapping the environment using a terrestrial, high-resolution 3D scanner
- Step 2: Creation of a 2D navigation map
- Step 3: Setting up the routes on site
- Step 4: Setting up the various coupling and uncoupling stations ("stations")
- Step 5: Test run and instruction in operation
-
How does the charging process work?
- Innok uses lithium-ion batteries so that the INDUROS can be in operation for up to 16 hours (depending on payload and route)
- The INDUROS is charged autonomously via an inductive charging station (advantage: no personnel required)
- Charging time: approx. 2 hours (from 20% to 80%), or 3 hours from 20 to 100% SOC (State of Charge)
-
Which languages can I select in the Innok Cockpit?
- The Innok Cockpit is currently available in the following languages:
- English
- German
- Innok Cockpit is browser-based and can therefore also be translated into other languages using the browser's automatic translation function. We cannot guarantee the correctness of the translation in this case.
-
Does the Induros recognize people and objects?
- Automatic stop and signal in the event of an obstacle (example video)
- Built-in high-precision safety scanner with a viewing range of at least 20 m and a viewing angle of 270°
- Automatic stop in the event of obstacles thanks to the Sick scanner suitable for outdoor use
- Bypasses are not programmed as standard and are not usually recommended by health and safety officers
- A permanent obstacle can be bypassed by remote control (or a bypass route can be defined in the user interface).
-
What safety features does an INDUROS have?
- Safety laser scanner with personal protection
- Emergency stop button
- Alarm module in the event of an emergency/fire alarm
- Rotating beacon
- Warning tone
-
What maintenance work needs to be carried out?
- The INDUROS is low-maintenance
- Depending on operation, scanner surfaces and tire pressure must be checked
- Minimal time required for dust removal and cleaning of cameras and sensors
-
How sensitive is the sensor system in general?
- All sensors and scanners are well protected on the robot. The safety scanner, for example, is also heated from the inside to prevent fogging. Under normal conditions, the laser scanner's own operating heat prevents fogging from the inside. It is also advantageous to have the robot in a hall overnight. If it is left outside all night and then moved into a warm hall, this can increase the risk of fogging.
- If the robot is used in an extremely dusty environment, there is the option of fitting an air shower on the outside for automatic cleaning.
-
What standards does the INDUROS meet?
- 2006/42/EC Machinery Directive
- DIN EN 1525: Driverless industrial trucks and their systems
-
What happens if the robot stops and nobody knows why?
- In such extremely rare cases, Innok Robotics technicians can connect to the robot via remote maintenance in the shortest possible time and rectify any problems.